silicon wafer is the main production material in semiconductor and photovoltaic field. silicon wire cutting technology is the world's most advanced silicon processing technology, it is different in the way of traditional saws, grinding wheel piece, cutting, is also different in advanced laser cutting and the inner circle cutting. its principle is through a high speed steel wire drives attached on the steel wire cutting edge material is used for friction on the silicon rods, to achieve the cutting effect. in the whole process, the steel wire through a dozen wire round of the guide, in the main line to form a wire mesh, and the workpiece to be processed through the work table to achieve the workpiece feed. compared with other technologies, the technology of multi wire cutting is more efficient, high productivity and high precision. is currently the most widely used in wafer cutting technology.
multi line cutting technology is silicon processing industry, solar photovoltaic industry landmark reform. it replaced the original inner circle cutting device, cutting chip and the inner circular slice process compared with the bending degree (bow), warpage (warp) small, parallelism taper, total thickness of public difference (tta) small discreteness, edge cutting loss, surface damage of shallow, wafer surface rough degree and so on many advantages.
solar wafer line cutting mechanism is the machine guide wheel in high speed driven by steel wire, thus by the steel wire will polyethylene glycol (peg) and sic powder mixed mortar sent to cutting area, high-speed operation in the steel wire and pressure on-line workpiece continuous friction finish cutting process.
in the whole cutting process, the quality of the silicon wafer and the finished product rate are the main effects of the viscosity of the cutting fluid, the particle size of the silicon carbide powder, the viscosity of the mortar, the flow of the mortar, the speed of the steel wire, the tension of the steel wire and the feed rate of the workpiece.
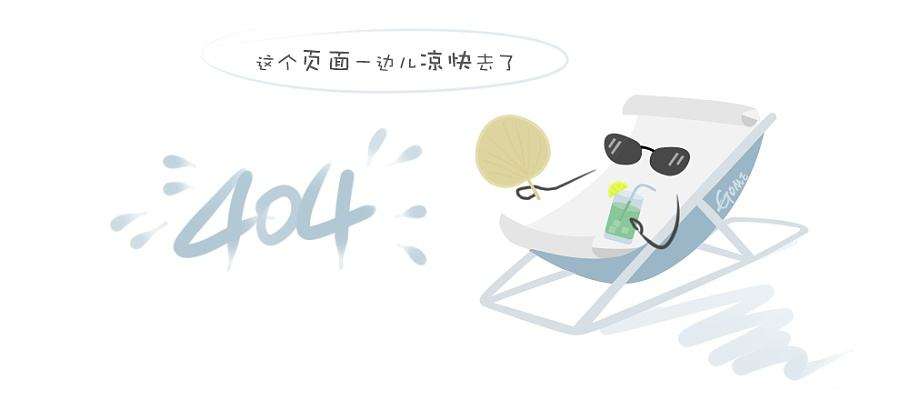
first, the viscosity of the cutting fluid (peg)
because in the whole cutting process, the silicon carbide powder is suspended in the cutting fluid through the steel wire cutting, so the cutting fluid mainly from the role of suspension and cooling.
1, the viscosity of the cutting fluid is an important guarantee for the suspension of silicon carbide powder. because of the different system thinking of different machine development and design, the viscosity of mortar is also different. for example, the swiss line cutting machine required cutting liquid viscosity of not less than 55, while ntc 22-25, ernst & young is as low as 18. only in accordance with the requirements of the machine to meet the requirements of the viscosity, in order to ensure the uniform distribution of silicon carbide powder in the process of cutting and mortar stability through mortar pipe into the cutting zone.
2, due to the steel wire with mortar in the process of cutting silicon material, because the friction occurs high temperature, so the viscosity of the cutting fluid plays an important role in cooling. if the viscosity is not up to standard, it will lead to poor liquidity, can not be reduced to the temperature caused by burning or broken, so the viscosity of the cutting fluid to ensure the temperature control over the whole process.
two, the particle size and particle size of silicon carbide powder
in fact, the cutting of solar silicon chip is a steel wire with silicon carbide powder in the cutting, so the particle size and particle size is the key to the finish and cutting ability of silicon wafers. laser scribing machine, grain type rules, cut out of the wafer that will finish is good; uniform particle size distribution, will improve silicon cutting ability.
three, the viscosity of mortar
wire cutting machine has an inseparable relationship with the viscosity of the mortar. and the viscosity of the mortar is depending on the silicon laser scribing machine cutting liquid viscosity, wafer cutting liquid and silicon carbide micropowder suitability, wafer cutting liquid and silicon carbide powder proportion, mortar density. only to meet the requirements of the machine to the standard viscosity of mortar (such as ntc machine requirements of 250) in order to improve the cutting process and improve the finished product rate.
four, mortar flow
steel wire in the high-speed movement, to complete the cutting of silicon material, mortar pump must be from the storage tank to play to the sand blasting nozzle, and then by the sand blasting nozzle sprayed into the steel line. whether the flow rate of the mortar is uniform and the flow can meet the requirements of cutting, it plays a key role in cutting ability and cutting efficiency. if the flow is not, there will be a serious decline in line cutting ability, sheet, break, or even machine alarm.
five, steel wire speed
as the line cutting machine can be carried out in accordance with the requirements of the user to go the line and the direction of the line, so the two cases of the line speed requirements are also different. when the direction of the line, the steel line has always maintained a speed (mb and hct can be adjusted according to the cutting conditions at different times), so relatively easy to control. at present, the operation of the one-way walk line is less and less, which is limited to mb and hct machines.
when the speed of the steel wire is accelerated to a speed of 0.2 seconds, the speed of the steel wire is accelerated to a specified speed, and then slowly decreases to zero along the direction of the zero, and then slowly decreases to zero. in the course of the two way cutting, the cutting ability of the line cutting machine can be improved with the increase of the speed of the steel wire, but can not be lower than the cutting ability of the mortar. stria and even disconnection occurs if the mortar is lower than that of the cutting ability; on the contrary, if beyond the mortar cutting ability may resulting in mortar flow can not keep up, and film thickness even stria tablets.
at present, the average speed of mb can reach 13 m / s, ntc is 10.5-11 m / sec.
six, steel wire tension
the tension of steel wire is one of the key elements in the process of silicon wafer cutting. tension control is not good, is an important cause of line edge collapse, even short-term.
1, the tension of the steel wire is too small, will lead to the increase of the bending degree of steel wire, with the ability to reduce the sand, cutting ability. which line etc..
2, the steel wire tension is too large, suspended in steel wire of the sic powder will is difficult to enter the zigzag cutting efficiency is reduced, stria etc., and disconnection of a great chance.
3, if the cut to the adhesive tape, sometimes because of the tension caused by the use of time is too long to cause the deviation from the zero point of change, the occurrence of collapse, and so on.
control of mb and ntc wire cutting machine general tension in the wire and wire is less than 1, only a difference of 7.5 ernst.
seven, the workpiece feed rate
the feed rate of the workpiece is related to the steel wire speed, the cutting ability of the mortar, and the different position of the workpiece shape. the feed rate in the whole cutting process is determined by the above factors, but also the most not quantitative one. but the control is not good, may also appear line films such as adverse effects, influence the cutting quality and yield.
in short, the operation of solar wafer cutting machine is an experience greater than the technical process and the standard of fine work. only in practice, constantly sum up and explore, in order to control the machine with ease.
solar photovoltaic network